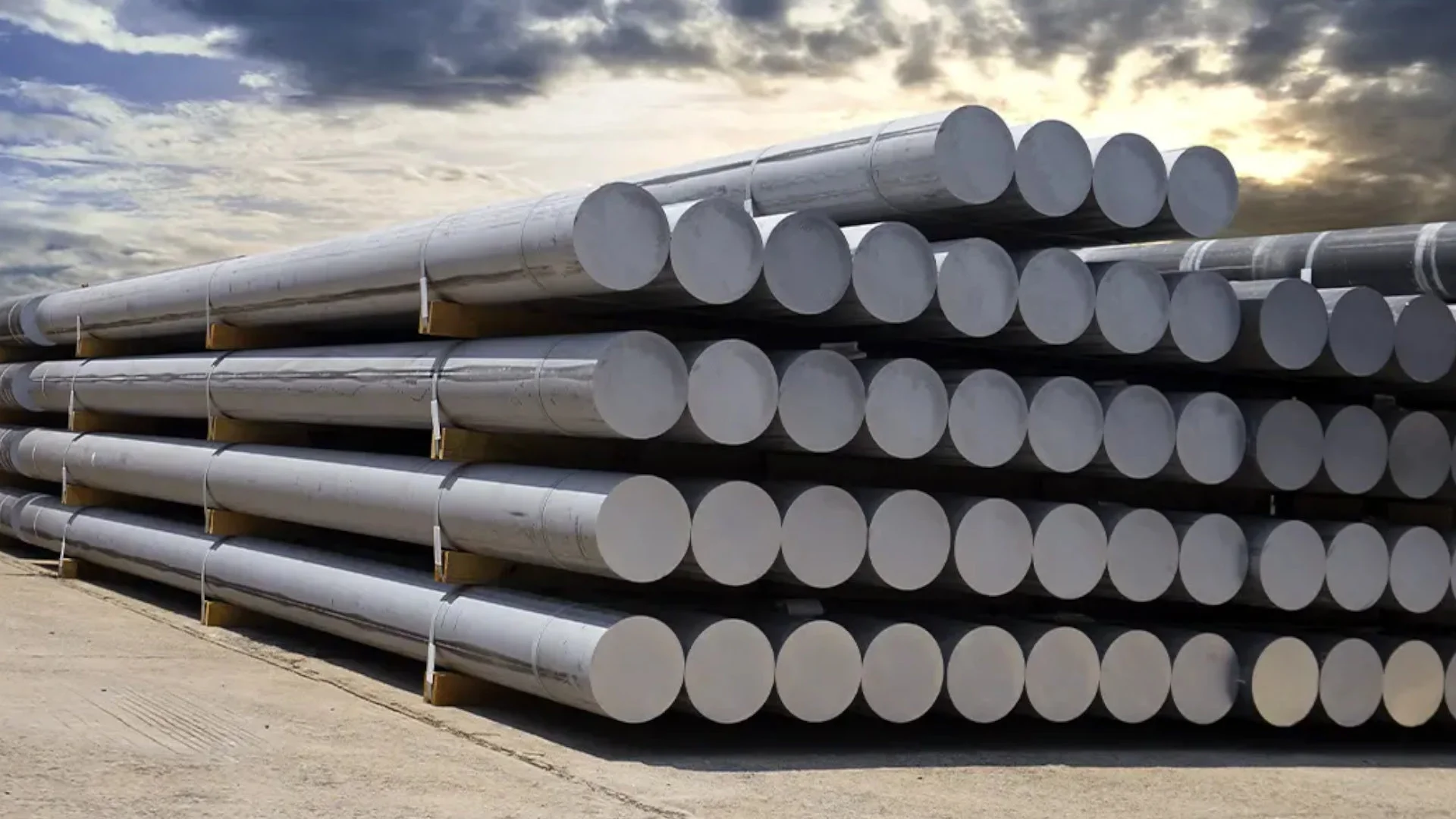
Le leghe di alluminio non sono tutte uguali, in base ai tipi di alluminio scopriamo insieme le caratteristiche meccaniche, chimiche e fisiche.
Le leghe di alluminio
Tra i principali scopi dell’uomo c’è la continua ricerca di produttività e funzionalità spingendolo sempre più nello studio, nella progettazione e nella realizzazione di qualcosa di nuovo sempre più funzionale per le esigenze del mondo che avanza.
Ha iniziato a modificare i processi produttivi per la sua sopravvivenza partendo dalle coltivazioni e dall’allevamento per massimizzare la produzione, fino ad arrivare ai grandi progressi tecnologici ed industriali degli ultimi 70 anni.
Nonostante l’alluminio sia un materiale giovane (con meno di 200 anni di storia) ha suscitato notevoli interessi e svariati impieghi portando ricercatori e produttori a modificare le caratteristiche chimiche e meccaniche per adattare l’alluminio ai più svariati campi d’impiego così da sfruttare le sue molteplici caratteristiche.
Oggi sul mercato sono disponibili una infinità di leghe di alluminio e altre continuano a nascere per soddisfare le richieste sempre più esigenti.
Ma scegliere la lega più adatta al proprio progetto non è cosa semplice perché a volte dietro alla presunta lega perfetta esistono delle difficoltà nel processo di fusione in fonderia o durante i processi dei vari trattamenti successivi, non ultimo la lavorazione meccanica.
Partiamo dall’inizio…
L’alluminio con purezza pari o superiore al 99% si presenta con limitata resistenza meccanica, buona duttilità, ovvero buona capacità di sopportare deformazioni plastiche, buona conducibilità sia termica che elettrica, eccellente resistenza alla corrosione ed elevata attitudine alla finitura superficiale.
Tutte queste caratteristiche non sarebbero bastate a far raggiungere all’alluminio la sua fama odierna.
L’alluminio raggiunge le sue più grandi performance nel suo utilizzo in fonderia quando viene unito ad altri materiali che vengono chiamati “alliganti” ovvero quando in esso viene disciolto un altro componente chimico, generalmente un metallo, per formare una lega.
Leghe d’alluminio: gli alliganti
La creazione di una lega con un altro metallo cambia le proprietà dell’alluminio, incrementandone la resistenza, la brillantezza, la duttilità, la fluidità e la lavorabilità all’utensile ad esempio.
I principali “alliganti” che vengono uniti all’alluminio per formare le varie leghe sono:
- il rame (Cu)
- il magnesio (Mg)
- il silicio (Si)
- il manganese (Mn)
- lo zinco (Zn)
- il ferro (Fe)
Ognuno di questi materiali, unito all’alluminio, ne conferisce caratteristiche meccanico-fisico che possono soddisfare le più svariate esigenze richieste oggi sul mercato.
Le funzioni dei materiali all’interno della lega
Silicio (Si): E’ il più diffuso legante dell’alluminio migliorando ampiamente le caratteristiche di resistenza e durezza, senza ridurne la duttilità.
La sua presenza diminuisce di poco la resistenza alla corrosione. Le leghe comunemente utilizzate in fonderia hanno contenuti che variano dal 2 al 15%.
Rame (Cu): Aumenta in proporzione alla quantità la resistenza meccanica e la durezza. Migliora la lavorabilità alle macchine utensili.
Diminuisce la resistenza alla corrosione, pur in piccole quantità. In quantità superiori al 12% la lega presenta una spiccata fragilità.
Magnesio (Mg): Conferisce alla lega un buon comportamento alla corrosione, infatti le leghe Al-Mg, in presenza di elementi alcalini o in ambiente marino, hanno caratteristiche anche migliori dell’alluminio puro.
Aumenta la resistenza meccanica e la durezza.
Migliora la lavorabilità alle macchine utensili e la duttilità.
Il magnesio migliora le caratteristiche meccaniche, a fronte di una diminuzione della colabilità della lega e di un aumento della fragilità da ritiro (per aumentarne la colabilità, alle leghe Al-Mg viene aggiunto silicio).
Nelle leghe di alluminio per fonderia la sua quantità può variare tra il 3 e il 10%.
Manganese (Mn): È principalmente impiegato come correttivo nei confronti del ferro, elemento indesiderato, svolgendo la funzione di tampone.
La sua presenza aumenta sensibilmente la tenacità, la duttilità e la resistenza meccanica e quella alla corrosione.
Zinco (Zn): È stato uno dei primi leganti dell’alluminio.
Viene utilizzato per aumentarne la resistenza e la durezza, ma determina una scarsa resistenza alla corrosione a fronte di una buona lavorabilità.
Si è cercato di eliminare tali difetti mantenendone i vantaggi mediante l’aggiunta di altri elementi in leghe complesse (leghe Al-Zn-Mg-Cu).
Ferro (Fe): Benché indesiderato, è sempre presente nelle leghe di Al come impurità. La presenza del ferro in quota dell’1% ha effetti positivi sulla resistenza meccanica.
È l’elemento più dannoso nelle leghe di alluminio in quanto i suoi cristalli provocano una disomogeneità nella sua struttura aumentando la fragilità del metallo e diminuendo notevolmente la resistenza alla corrosione.
Titanio (Ti): Aggiunto solitamente nella lega di alluminio come affinante del grano metallico, riducendolo, rendendo il metallo più compatto.
Il quantitativo è solitamente inferiore al 0,25%.
Stronzio (Sr): l’introduzione nella lega fa sì che si formino particelle di silicio globulari e molto fini aumentandone la tenacità e la lavorabilità.
Riduce la tendenza alla formazione delle cavità da ritiro.
Le principali norme
“Le leghe di alluminio vengono regolamentate da norme Italiane, Europee ed Internazionali”.
UNI EN 1706 è la Norma Europea per la designazione di Alluminio e leghe di alluminio – Getti -Composizione chimica e proprietà meccaniche per le leghe da fonderia approvata il 2 marzo 2020 che sostituisce la UNI EN 1706:2010.
Questa norma specifica i limiti, minimi e massimi, di composizione delle varie leghe di alluminio per getti e le proprietà meccaniche delle provette colate a parte per tali leghe.
Secondo la Direttiva Europea 98/34/CE del 22 giugno 1998: La “norma” è la specifica tecnica approvata da un organismo riconosciuto a svolgere attività normativa per applicazione ripetuta o continua, la cui osservanza non sia obbligatoria e che appartenga ad una delle seguenti categorie:
Norma Internazionale indicata con la sigla ISO ( International Organization for Standardization): Identifica tutte le norme elaborate dall’organizzazione internazionale per la standardizzazione.
- Sono norme valide in tutto il mondo.
- Queste norme sono un riferimento applicabile in tutto il mondo.
- Ogni Paese può decidere se rafforzarne ulteriormente il ruolo adottandole come proprie norme nazionali, ad esempio in Italia la sigla diventa UNI ISO;
Norma Europea indicata con la sigla (EN): Identifica le norme che vengono approvate dall’Organismo di Normazione Europea (CEN – Comité de Normalisation Européen).
- Le norme EN devono essere obbligatoriamente recepite dai Paesi membri CEN e la loro sigla di riferimento diventa, nel caso dell’Italia, UNI EN.
- Queste norme servono a uniformare la normativa tecnica in tutta Europa, quindi non è consentita l’esistenza a livello nazionale di norme che non siano in armonia con il loro contenuto;
Norma Nazionale (UNI) che indica la sigla dell’ Ente Nazionale Italiano di Unificazione che elabora e pubblica norme tecniche per tutti i settori industriali, commerciali e del terziario contraddistingue tutte le norme nazionali italiane e nel caso sia l’unica sigla presente, significa che la norma è stata elaborata direttamente dalle Commissioni UNI o dagli Enti Federati.